Creating a culture of safety is an important and ongoing topic in the manufacturing sector. Keeping employees and others safe should always be at the forefront of your mind. Unsafe work environments create an incredible physical, emotional, and financial toll on employees and the company at large. Staying in business, having a good reputation, and being profitable can all be linked to the culture of safety a company has implemented.
A culture of safety can be defined as, “the way safety is perceived, valued, prioritized, and integrated in all activities in the workplace. It’s the set of core values and behaviors that make safety a priority.” In other words, safety needs to be on top of mind for all employees from the beginning to the end of their shift.
Importance of a Culture of Safety in Manufacturing
There are many benefits to creating a culture of safety within your business or manufacturing facility that will pay off long-term. Prioritizing safety prevents injuries, increases efficiency, boosts productivity, and benefits worker confidence and retention. To be blunt, you cannot afford to not care about creating a culture of safety within your organization.
Many strategies can be used to create an effective culture of safety within your organization. Though they may vary, depending on industries and regulations in place, all should include these 6 integral elements.
6 Elements to Create a Culture of Safety
1. Risk Assessment
The first step in creating a culture of safety is to get a complete overview of current conditions and do a risk assessment. This will give you a baseline of where the company is at and where protocols should be placed first. Risk assessment is the foundation for the safety strategy and once complete, you can start to build toward a culture of safety that works for your company.
The risk assessment can also help with collecting data about previous safety incidents and the machinery most likely to cause these incidents. You can use this information to share with employees, so they have knowledge of which machinery to take extra precautions around. You can also use this information to create extra labeling and signage around the areas that have a higher incident rate.
2. Communication
Communication is the next element that is essential in creating a culture of safety. There is no replacement for great communication between leadership and employees. To ensure that workers understand the goals and policies that are put into place for the safety strategy, it is best to communicate about them frequently.
Some organizations hold weekly, bi-weekly, or monthly meetings or safety sessions to highlight different parts of the culture of safety strategy. Some even highlight safety at the beginning of each shift. Do whatever works best for your company, but make sure that safety is being communicated to employees frequently. This communication helps to establish the culture of safety as a core part of the values and beliefs of the company.
3. Training
Training is like the communication element of the culture of safety, but with a more hands-on approach. After everything has been communicated, you can use training to show employees how to apply the safety protocols in real-time. They can gain a greater understanding of the risks that may be associated with different machinery and how to avoid simple mistakes that can lead to injury or an unsafe work environment.
Moreover, it is best to make the training as engaging as possible for employees. You do not want this to be wasted time for leadership or employees. Keeping the training engagement up helps to show that employees are valued by the company, want to keep them safe, and give practical tips that can be used right away. This is especially important when new machinery is introduced so that all workers have a good understanding of how it functions and any new safety concerns that may arise.
4. Management Involvement
Creating a culture of safety cannot be completely implemented unless management and leadership are fully behind the strategy in place. Management sets the tone for the company and the values you want to uphold. If safety is important to leadership, it will be important to the workers that work under them.
With management fully on board, it will increase the employees’ trust in leadership and the company, in turn making communication and training more effective. Have leadership lead by example with all protocols and recognize employees that are doing that as well. Set high but attainable standards for your team and motivate them to continue to follow the safety strategy.
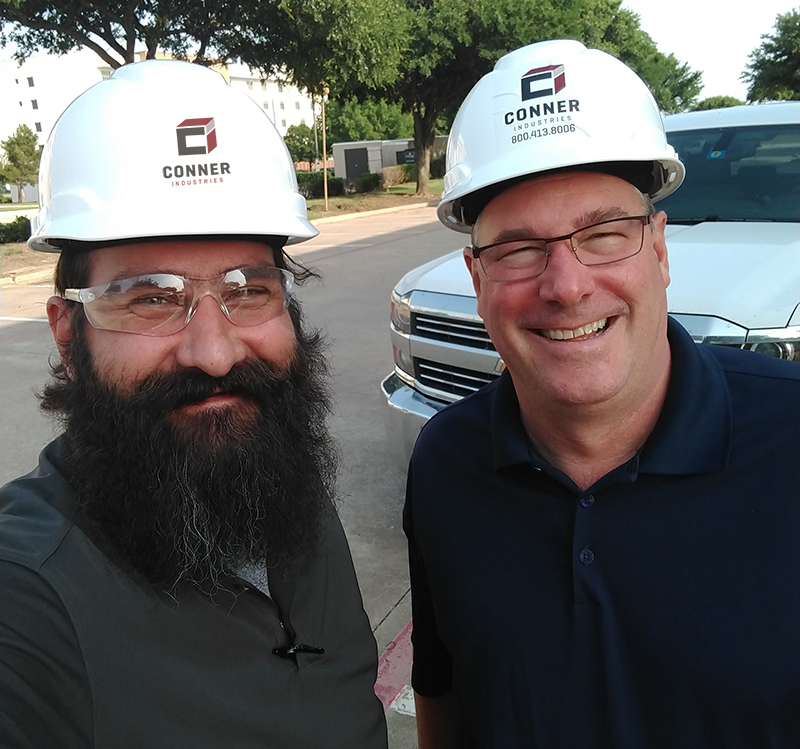
5. Report Incidents Properly
Reporting incidents and concerns will be an important part of maintaining a culture of safety once you have established it. Team members should feel safe identifying and reporting any safety concerns they may have, without fear of retaliation or punishment. An effective culture of safety is one where employees are engaged in good safety practices and vigilant for any hazards. In safety meetings, you can use the reported incidents to make changes and enhance the safety strategies in place.
6. Be Solution Focused
The last way to create a culture of safety is to be solution focused at all times. Once you know of a risk, there needs to be a solution in place to prevent any further issues. Changing your mindset to instantly think of solutions will help to keep everyone safe and the production line moving.
Put a process in place for what happens after incidents are reported and how the solution will be carried out. Handling each safety concern in the same, solution focused way will continue to solidify good internal communication between leadership and employees.
Conner’s Commitment to Safety
Conner Industries is a leading provider of industrial wood and packaging solutions. We specialize in supplying cut lumber needed for pallets and transportation packaging, fully assembled custom pallets, crates, and integrated packaging. We serve customers nationwide from our 14 locations, so you always have packaging solutions you can count on.
With over 40 years of experience, Conner has created a culture of safety that keeps employees safe and healthy- while taking care of our customers. We have dedicated positions that uphold the culture of safety we have created and help keep safety top of mind for all employees. We are always looking for ways to innovate and become even better as we continue to grow.