Unless you work in the packaging industry, you probably have no idea that there are several different packaging types and categories that meet very specific needs. In fact, each of these packaging categories is so different in purpose and materials, as well as how products are packed and shipped, that they each have an industry of their own.
What can also make packaging types confusing is that they are often called different things, depending on who you’re talking to about it. It can all get pretty confusing, which is why we’ve decided to try to clear things up for you here.
So let’s talk packaging types.
The Main Packaging Types
In general, there are three levels of packaging, and they’re called Primary, Secondary, and Tertiary. Each of these packaging types has a different purpose, they’re made from different materials, they’re packed and shipped differently, and they’re seen by different people in the marketplace.
Innermost Layer = Primary Packaging
As consumers, primary packaging is the packaging type that’s most familiar to us, but it’s also the type of packaging that we do not produce here at Conner. Primary packaging is the packaging that most closely touches the product, and it’s often referred to as retail packaging or consumer packaging (packaging for Consumer Packaged Goods or CPG). Primary packaging is literally the last bit of packaging between the product and the end-user. It’s generally only used in Consumer Packaged Goods, which are goods that customers use up and replace frequently.
Here are some examples to clarify the primary packaging concept:
You get the idea here. Primary packaging holds the product and protects it, but it also has another purpose. Primary packaging is also designed to attract customers to the product.
You can kind of think of it as utility meeting marketing.
The most important job of primary packaging is to protect the product so that the end-user can… you know… use it. Poorly designed protective packaging impacts the end user’s ability to use the product. In the case of perishable goods, defective primary packaging can make the product completely unusable (or even dangerous), but even non-perishable goods can be damaged if the primary packaging doesn’t do a good job of protecting the product.
Primary packaging that doesn’t do an adequate job of protecting the product will eventually push customers toward competitor products. That’s pretty obvious.
What is less obvious is how much products and the company can be affected by poorly designed primary packaging from a marketing perspective. Primary packaging usually displays the company’s logo, branding, and slogan in a way that’s pleasing to consumers and advertises the product. It’s a way to help identify products in the marketplace and distinguish the company brand.
Failure to attract customers with well-designed primary packaging is certain to affect company sales and the company’s bottom line.
Secondary Packaging Layer For CPGs
Secondary packaging is the next layer of packaging and is used to ship products that are already secured within their primary packaging. Secondary packaging is the packaging type that holds the individual product units together. The main goal of secondary packaging is to protect the products, the primary packaging, and provide branding during shipping.
Secondary packaging is often used as display packaging in retail locations, such as grocery stores and warehouse stores, and sometimes secondary and primary packaging can overlap. In general, secondary packaging should be tough enough to protect the product, yet easy enough for the end-user to open.
Here’s an example from consumer packaged goods. Beer comes in the primary packaging of a can or bottle, and it has secondary packaging of the cardboard box that the cans or bottles are shipped in. In this case, the two types of packaging definitely overlap. Not only do the bottles (primary packaging) have the company logo and branding, but the box that holds the bottles (secondary packaging) does too.
Again… Conner does not produce this kind of secondary packaging.
Secondary Packaging for Non-CPG Manufacturers
If you don’t manufacture consumer packaged goods, like the soda, potato chips, dish soap, flash drive, doll, or beer we talked about earlier, then secondary packaging is a bit different. Regardless of the product, secondary packaging facilitates the transportation of a product from the manufacturer to the end-user, but for non-CPG manufacturers, secondary packaging isn’t seen by the ultimate end user.
For this packaging type, that means that manufacturers don’t usually bother with marketing messages or company logos on their secondary packaging (although some do too). In this case, secondary packaging is more about utility than marketing. It also has to be strong enough to protect the product, yet easy enough for employees to open without damaging the product.
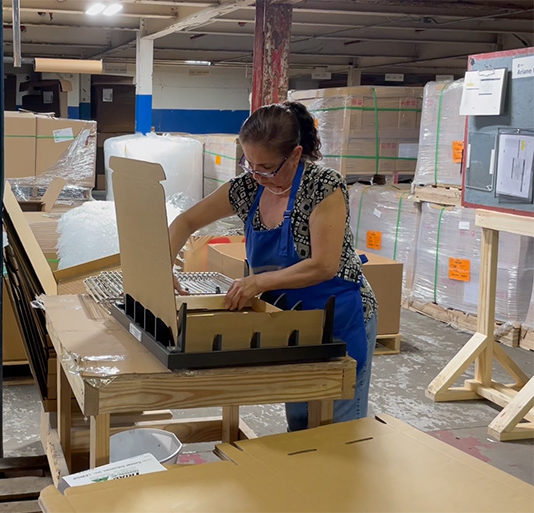
This is where things can get a little bit confusing, especially if you’re not part of the packaging industry, so let’s look at an example. Let’s look at a large home appliance, like a refrigerator.
If you manufacture refrigerators, you don’t just load your shiny new appliances on a truck and send them to a big box store. That would invite all kinds of damage in transit.
Instead, each fridge must be individually wrapped in protective packaging, also called secondary packaging or integrated packaging. Then each packaged fridge is packed into another layer of protective packaging (we’ll talk about tertiary packaging in a minute), before being transported to the end-user. Secondary packaging should be tough enough to protect your item, and yet easy enough for the employees engaged in restocking, repackaging, or installation to access your product without damaging it.
Going back to the refrigerator example, when the fridge shipment reaches its destination, each product will likely be unloaded into a warehouse until it is sold from a showroom. Once a consumer buys one of the fridges, the refrigerator, including the secondary packaging, will be delivered to the end-user. That secondary packaging protects the individual refrigerator while in transit to the consumer. The employees doing the installation will remove the secondary packaging on-site, usually in the back of the truck, before bringing the refrigerator into the house and installing it in the kitchen.
For all intents and purposes, the end-user never sees that packaging at all. They only see the shiny new refrigerator being installed in their home.
This type of integrated packaging (or secondary packaging) has a lot of other uses in manufacturing. For some manufacturers, the end-user is another manufacturer or industry. Take the automotive industry for example. Lots of different manufacturers make sensitive, fragile, or small component parts for the automotive industry.
Once manufactured, components must be packed into secondary packaging to protect them, before being put in tertiary packaging to ship them to the automotive manufacturer for use. The end-user, the automotive manufacturer in this case, then unpacks the secondary packaging to install the component onto one of their vehicles.
This type of secondary packaging must be engineered to protect the components, thus the reason why it’s also called integrated packaging. It usually consists of a combination of wood, corrugate (cardboard), foam, and plastics.
Outermost Layer = Tertiary Packaging
Finally, we get to the last layer of packaging, called tertiary packaging. This is the outermost layer of packaging that’s most often used by warehouses and manufacturers to ship the products (which are already wrapped in secondary packaging). The primary goal of tertiary packaging is to protect shipments during transit.
This type of packaging is rarely seen by end-users and includes pallets, wood crates, banding groove lumber, strapping, stretch wrap, etc. Here at Conner, the primary component of our tertiary packaging is wood, but tertiary packaging could even include large shipping containers used on ships and rail.
Why Does It Matter?
Understanding packaging types can be a bit confusing, especially if you’re not in an industry that readily deals with packaging. It’s clear that each of the packaging types is vastly different, so it’s important to understand the differences.
When you’re working up a packaging strategy, it’s also pretty important to think about each level of your packaging in order to make sure that your products will be protected and that you’re taking the total cost of your packaging into consideration before committing to a course of action.
Obviously, choosing the wrong packaging solution will likely result in all kinds of in-transit damages. On the other hand, making the right packaging solution choice will not only protect your products but will also optimize your supply chain.
*Updated 6/20/2023*